
The following diagram was made using data from my own car, which has been lowered and has modified strut tops providing more castor. It would seem these are all things that could be related to poor anti-dive geometry. A few problems here and there losing traction on the rear end when braking hard, and the dreaded delay when hitting the brakes to try and get some weight on the front end, it’d take a moment before the weight hit the tires. It had often bothered me that despite having the car sprung relatively hard it was still a bit doughey when jumping on the brakes. I must admit this is not really something I had ever considered, but after looking into it it became clear further investigation was needed. In an IRS car, the engine torque reaction is completely resolved at the differential's chassis mounting and never gets past all those U-joints to the wheels.Image (17) 1920×1440 148 KB How does it look on the Sirion chassis? Losing the front bar achieves a similar effect. They work in a stick-axle car by carrying back more of the engine's torque reaction and using it to "re-plant" the RR tire for more even side to side grip (and a little more in total). Incidentally, adding a huge rear antiroll bar generally isn't the answer for an IRS car. After that, down she comes taking some forward bite along with it. More that 100% means 'separation' for as long as there's enough bite and axle torque to maintain it.
ANTISQUAD LINE HOW TO
I'm not seeing big increases in A-S for the S550 until/unless somebody figures out how to relocate an LCA pivot without completely hosing other geometric effects.įWIW, 100% A-S means no squat on launch and no delayed help form springs or shocks. In the S550's integral link IRS, anti-squat is primarily determined by the LCA, with (I think) a small contribution from the integral link's orientation as well. This means that the slope of the IRS construction line is much gentler (lower anti-squat %). One is that for IRS, the anti-squat construction line passes through the axle centerline (side view here), where the stick-axle line starts much lower at the contact patches.
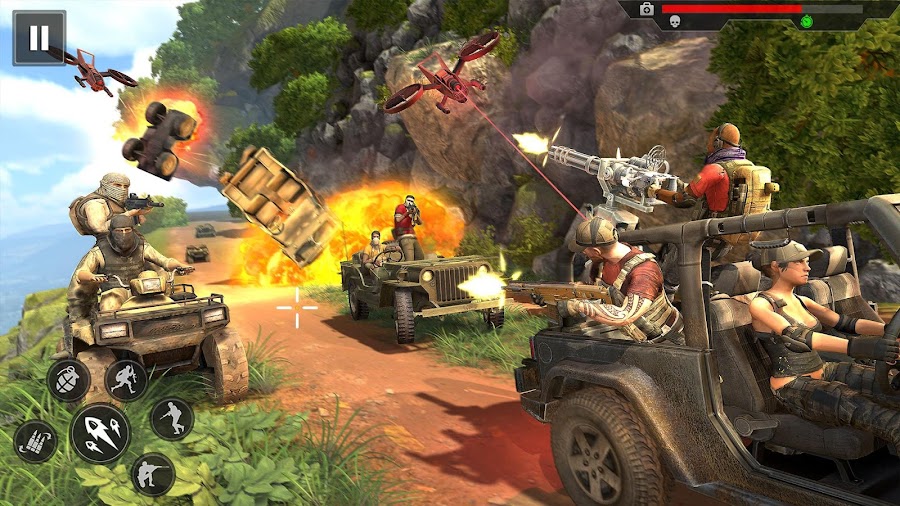
This approach isn't as applicable to most IRS designs for a couple of reasons. It's really easy to build anti-squat into most stick-axle suspension arrangements by simply relocating a few linkage pivot points. Shocks resist force in proportion to suspension velocity, which peaks somewhere between the other two effects. In between are the effects of rear shocks.
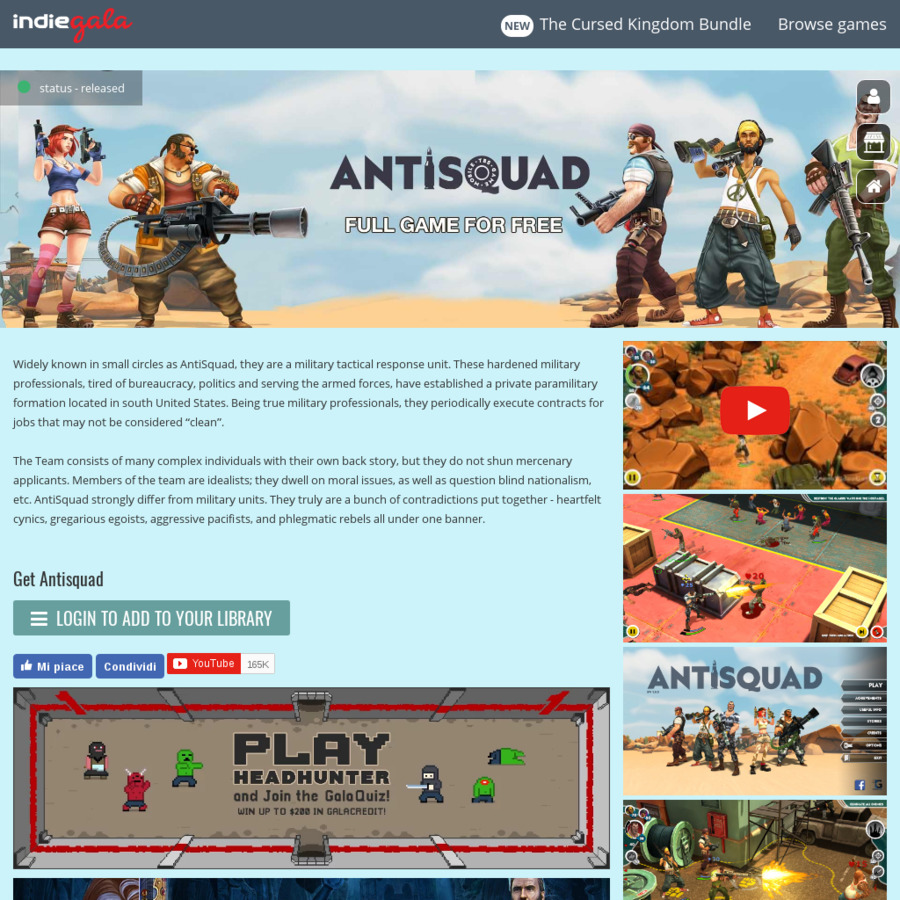
Plenty of time for incipient wheelspin to go all loose on a hard launch in the absence of sufficient anti-squat help. Since the spring (and wheel) forces from this effect do not fully develop until the suspension has found its new, lower equilibrium ride height, this takes a bit longer, perhaps a third of a second or so.
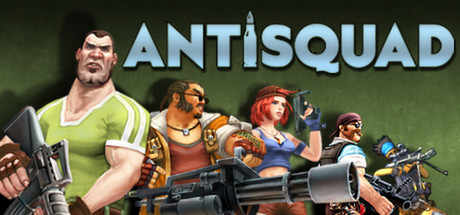
What the actual anti-squat effect is, is to allow near-instantaneous rearward load transfer directly to rear tire vertical loading and rapidly increase the amount of available forward bite.īut anti-squat (geometric load transfer, to a suspension engineer) is only one of at least three effects that are going on.Īnother involves the suspension spring stiffnesses (perhaps more accurately, rear suspension wheel rates). As you are probably aware, anti-squat is a rear suspension side view geometry thing, roughly defined as "resistance to squat during rearward load transfer".
